Technology is a grand thing. Thanks to these cool items we live a more comfortable life and businesses can dodge such issues as labor shortages.
A variety of new-guided vehicles have been introduced recently that assists warehouses overcome productivity problems when there are labor shortages. Lack of skilled labor has been plaguing the warehouse trade for several years. And it’s been made worse thanks to the Covid-19 Pandemic.
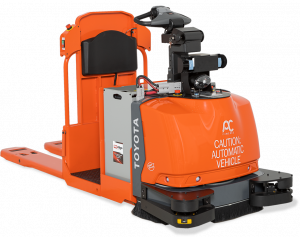
(Courtesy: Toyota Forklifts)
Warehouse managers are focusing on a few automated material-handling alternatives that help to solve certain warehousing issues and assists companies to achieve business growth. Each permits 24/7 productivity, lowers labor costs, reduces manual processing and mistakes and even enhances worker ergonomics and safety.
The equipment includes:
• Automated Guided Vehicles (AGVs) for transportation purposes
• Automated Storage and Retrieval Systems for storage
• Automated Sorting and Sequencing for picking
Automated Guided Vehicles For Transportation
Usually referred to as AGVs, these items are essential in performing incoming and outgoing material handling. They are used to move products that arrive at the warehouse and needs to be inventoried. They are also used for picking products from storage. These items come in different sizes, types, and navigation options.
Vehicles associated with this category include:
• Pallet transport AGVs that serve as driverless forklifts.
• Toting transport AGVs for carrying lighter loads through the process.
• Cold storage AGVs that serve in chilled or refrigerated conditions.
These solutions have advantages to other transportation machinery. They use less space than conveyors, are energy efficient, can be changed or reprogrammed to satisfy different conditions as a business changes, and they include highly tech safety features to enhance ergonomics and decrease hazards.
Automated Storage and Retrieval Systems for storage (AS/RS)
Many warehouses today are overwhelmed with products. As a result, they need ways to maximize floor space and still maintain easy access to inventory. Automated Storage and Retrieval Systems are adaptable to different storage space options, reduces picking time, minimizes the manual process and permits easier inventory control. Particular models of these systems support different load sizes, maximum heights, and load types. They include:
• Pallet Storage AS/RS support the storage of heavy unit loads, expanding the use of available space within the warehouse.
• Case and tote storage AS/RS permits the storage of a large number of SKUs, making sequencing easier and delivering products to pick stations.
• Shuttle-based Storage AS/RS work well for storing and fetching goods without error and speeding up fulfillment with lower SKU counts.
These systems can support a wide assortment of products and can operate in different types of facilities and under diverse conditions. This is beneficial for the cold supply chain because it prevents the use of workers in frigid environments. Besides providing comfort for the personnel, this assures that refrigeration systems operate more efficiently.
Automated Sorting and Sequencing for picking
Usually, sorting and sequencing are tasks that are done manually. They require the workforce to do time-consuming physically repetitive tasks. The time workers spend walking through warehouses can account for more than 50 percent of total picking time.
Automation allows workers to be more productive and decreases the need for human intervention. Automating the carry of goods in between processes or from storage to personnel can make a warehouse much more efficient.
This category includes such vehicles as:
• AS/RS + Rail-Guided Vehicles that offer high speed sorting for complex pallet handling systems. It’s ideal for quickly transporting heavy loads between procedures.
• AS/RS + Case Sorting Vehicles enhances productivity by automatically moving products to personnel.
• AS/RS + AGVs allows for the transportation of goods to workers or in between procedures. It helps improve flexible travel paths and confined spaces.
To achieve the most ROI automation equipment should be integrated into larger systems that are flexible so that they can support future growth.
These systems can be placed alongside pre-existing systems and can be integrated with your current set up.
(Source: dcvelocity.com)