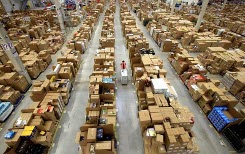
When things are good you have a smooth operation, the links in the supply chain work hand-in-hand; together producing a well-oiled machine. However, when things are bad — you quickly realize just how much you depend on a steady and consistent supply chain.
Risk Management is something that a lot of companies do not like to study. There might be a number of reasons for this avoidance, however if you could point the blame to one factor, it’s likely that managers and company owners hate to dread the worst case scenario. Right now sales are stellar and your warehouse is operating proficiently. Why dwell on the negative? The problem with this approach is that when things do not go as planned and, they inevitably will, managers are stuck with their hands in their pockets essentially thinking, ‘Okay, now what?’
Risk Management, therefore, is vital. You must understand that the importance of having a Plan B is second to none. You must be flexible and then, when the problem arises, you are prepared to handle it.
There are a number of factors which contribute to a break in the supply chain: political disruption overseas, natural disasters, the economy, war and regulation are just a few of the factors which can disrupt the normal chain of events. Due to all these concerns, Risk Management is essential for any savvy business owner, material handling not excluded. Take the time to make sure you think of those worst case scenarios so you are prepared for a Plan B when things fail. What will you do if the forklift you depend so much on breaks down in the middle of a key shipment? If you’re short on pallets and quickly find you need to drop off product, do you have a backup storage option?
It’s simply Murphy’s Law… “If something can go wrong it will go wrong”
Risk Management is the act of realizing that things will eventually go wrong, and taking steps to minimize the consequences of those risks. Plan for the worst, and when things fall apart, you’ll be prepared to handle the situation. It’s the simple steps which separates a good company from a great one.
If you spent a lot of time in a warehouse you understand that it’s a large place with plenty of complexity. There are a number of parts and people who come together to make it work effectively. Unfortunately, vehicles break down, supplies get used and beaten up, parts break, people get sick, emergencies arise and a number of ‘worst-case situations’ evolve over the course of an operation. If your budget will allow, always plan to have extra material.
Ask yourself what would happen to your business if there was a break in your supply chain: Do you have another supplier you could turn to? Do you have enough parts to see you through, in case a delivery was delayed?
A proficient business, therefore, is one which takes every precaution to avoid a major break in the supply chain. There will always be short-term, minor breaks in the chain. It’s an inevitable piece of the industrial puzzle. However, avoiding the major, long-term breaks is what ultimately keeps a good company moving forward and surviving for years.