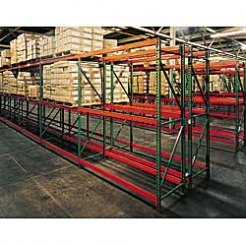
One of the most important duties of a warehouse worker is picking orders. That’s because a warehouse spends more time on the outbound transactions than the inbound. Moreover, the labor in performing the task is extensive and could be the largest portion of a warehouse’s labor budget.
There is another element that makes picking orders important. It is directly related to customer satisfaction. A person who purchases a product, no matter how large or how small, wants it delivered yesterday. They won’t tolerate waiting days or weeks for their order to arrive.
So it is imperative that the elements of a pick – speed and accuracy in picking and processing the order properly — makes the chore the most critical aspect of a warehouse’s business.
There are three methods of picking orders –- piece picking, case picking, and pallet picking.
Which method you use depends on the products being picked, total number of transactions in an order, total number of orders per shipment, picks per order, quantity per pick, picks per SKU, total number of SKUs, value-added processing (for example, private label), and the manner in which the order is picked in each method. Software is available to analyze each measureable to help you decide on what picking method is best for you. Many times a warehouse manager will discover that it is more profitable and efficient to combine picking methods.
Things one considers when selecting a picking method include increasing productivity and accuracy and reducing cycle time.
One measures productivity by the pick rate. The amount of time to get an order from entry to shipping is cycle time. Accuracy, of course, pertains to picking the right SKU for each order. A number of technologies exist that assists in this including pick-to-light systems, counting scales, and bar code scanners.
Proper training of personnel, precision in tracking, and accountability are what is necessary in achieving the goal of high-level accuracy.
Achieving the utmost efficiency is essential regardless of the method of picking you use. So products that are most frequently picked should be the easiest to access and located as close to the pick point as possible. Each SKU should have its own designated area. In addition, there should be a reserve or overflow storage area. A replenishment system should be created to move product from other locations in the warehouse to the fixed picking location as inventories dwindle to predetermined numbers.
There should be a checkout location for all outgoing shipments where one or more workers can ascertain that the order has been properly picked.
During the next few weeks I will be describing each method of pick ordering including piece, case, and pallet. I will also describe the best equipment to use for each method.
Keep note as you read each blog that no method may be absolutely perfect for your operation. At times there may be elements of a method that conflicts with other elements causing affects on productivity, cycle time, or accuracy. Under these circumstances you may have to tweak somewhat the method you select to ensure optimum performance.